Adding new life to walls and balcony decks in 200 units
Dixon Landing
Milpitas
Often times, when working on an apartment complex, not only do you need to coordinate the installation, but you also want to be mindful of making as little disruption for the residents as possible.
Working on 200 units in 29 buildings plus balcony decks and carports, our team definitely had our work cut out for us, but luckily this project was a great fit for a team like ours that specializes in these types of projects!
Not every project has the building coating and deck coating; this extra scope brings in our deck coating team to follow the painting.
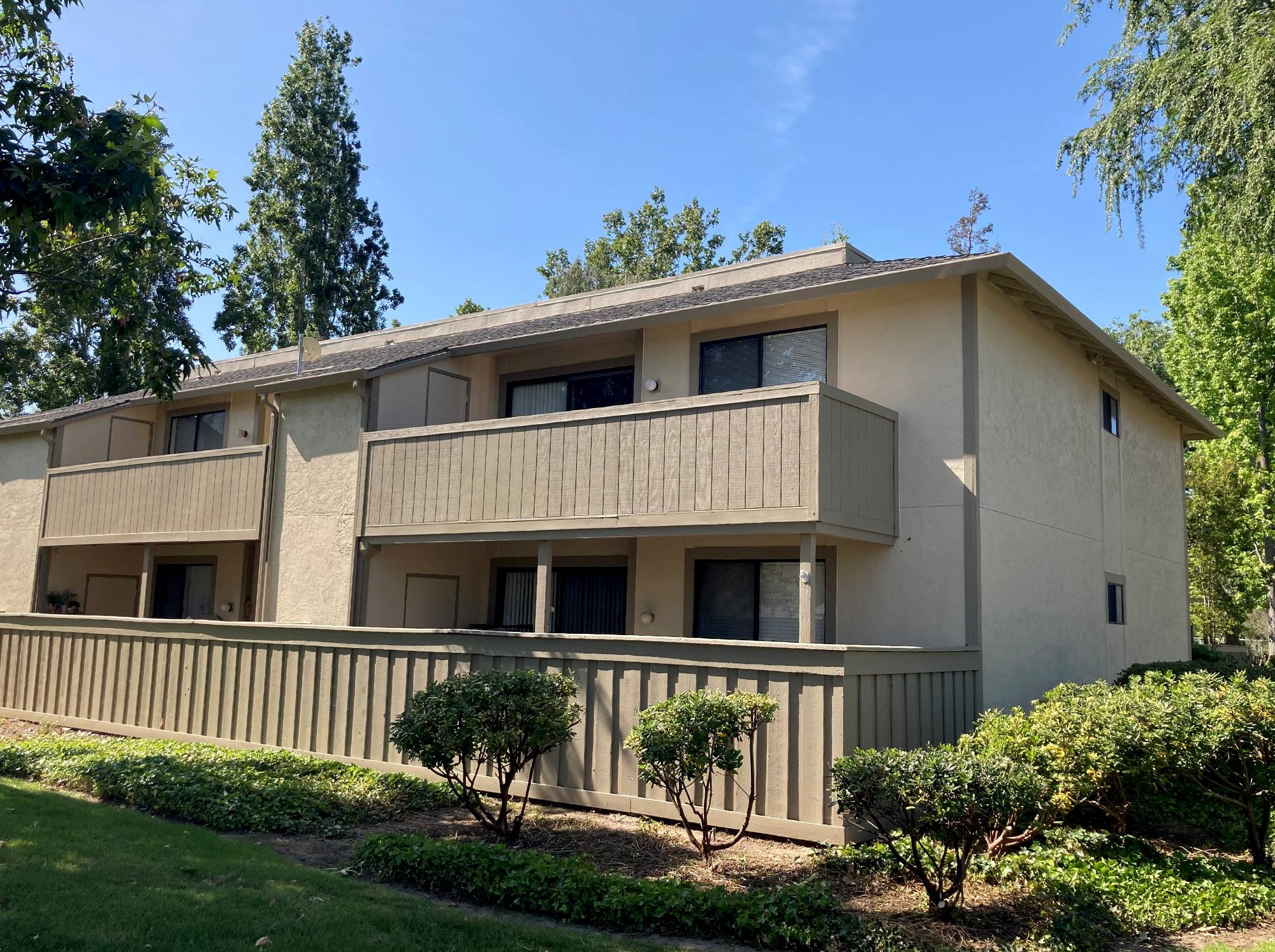
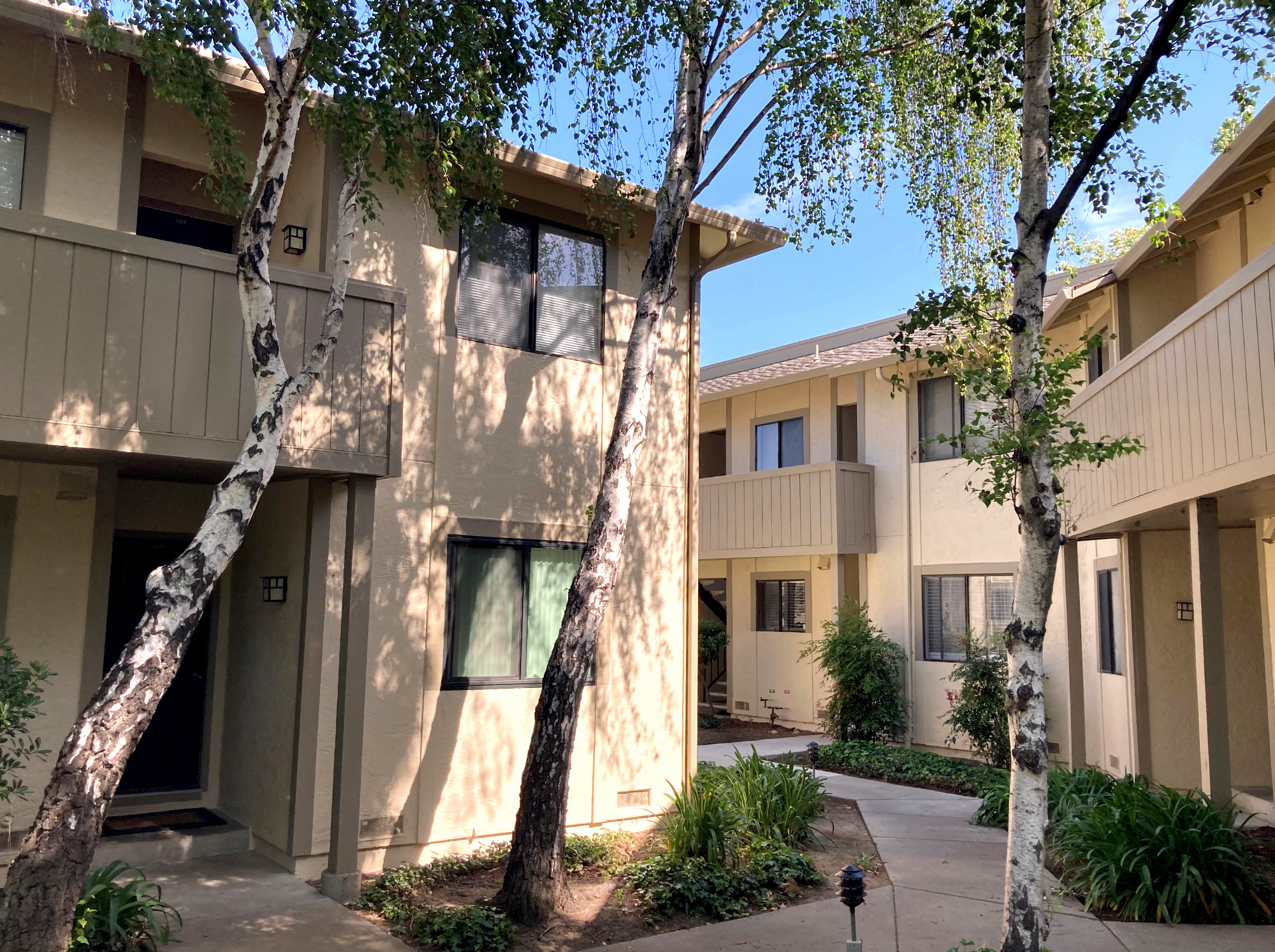
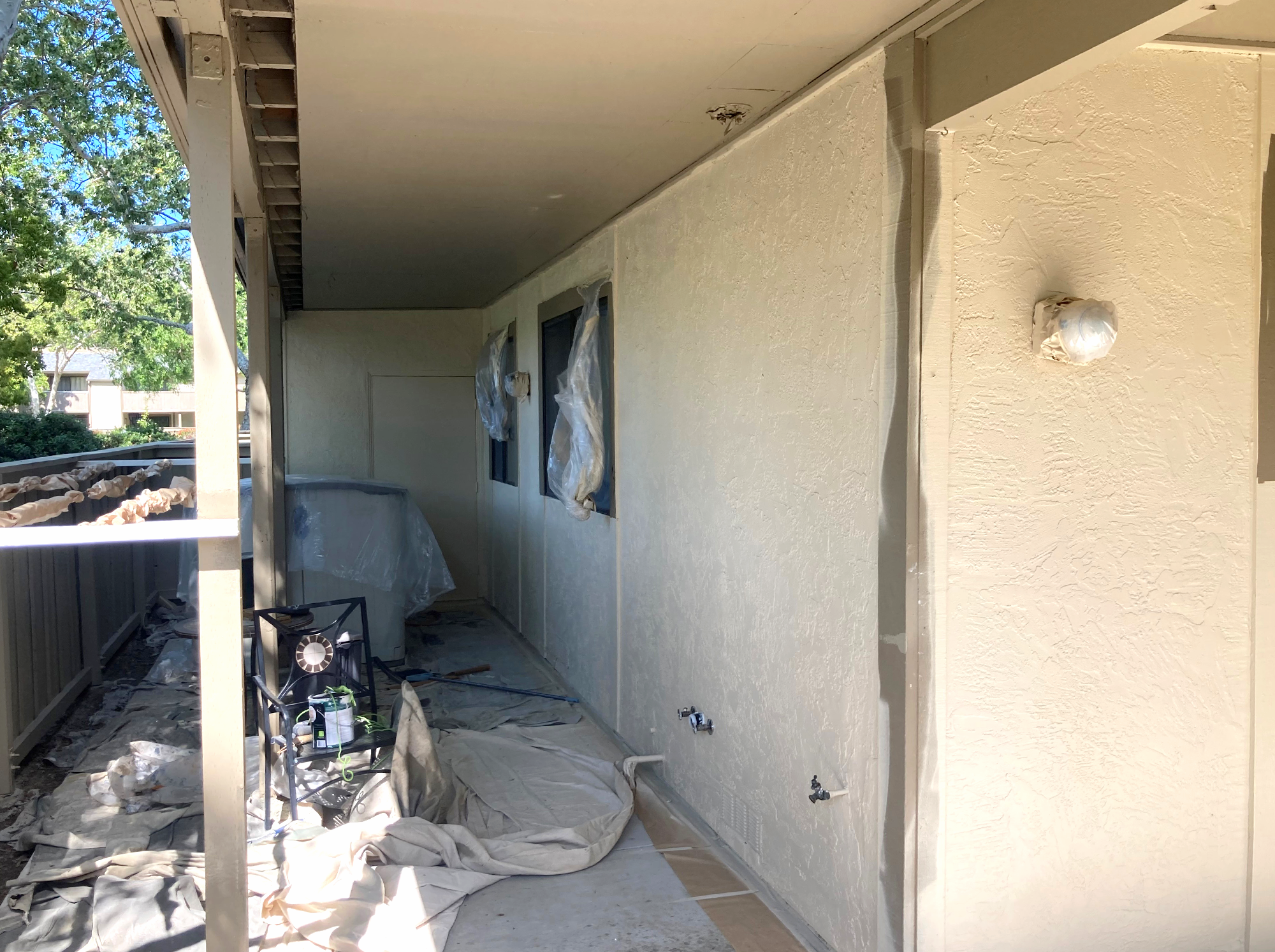
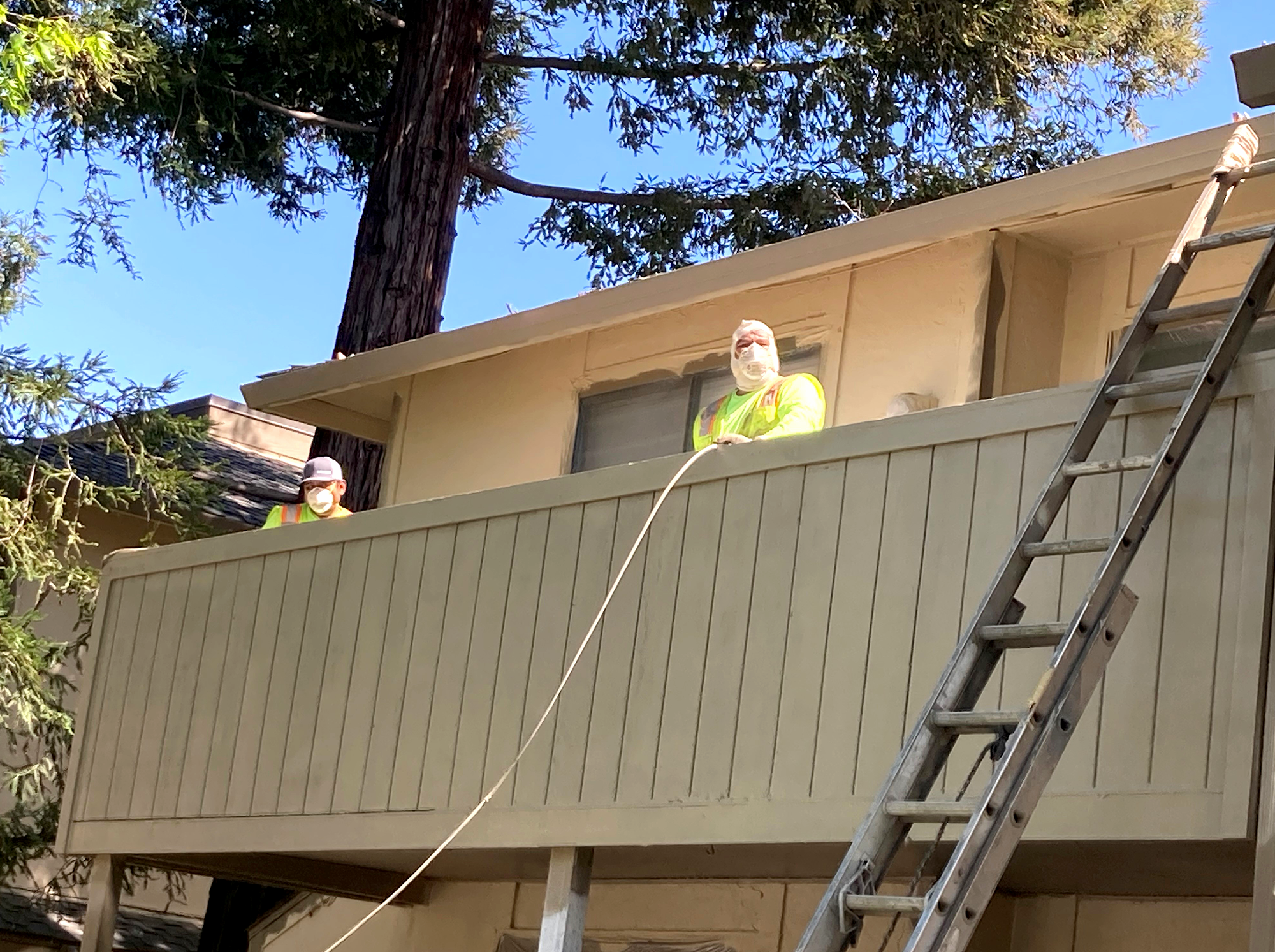

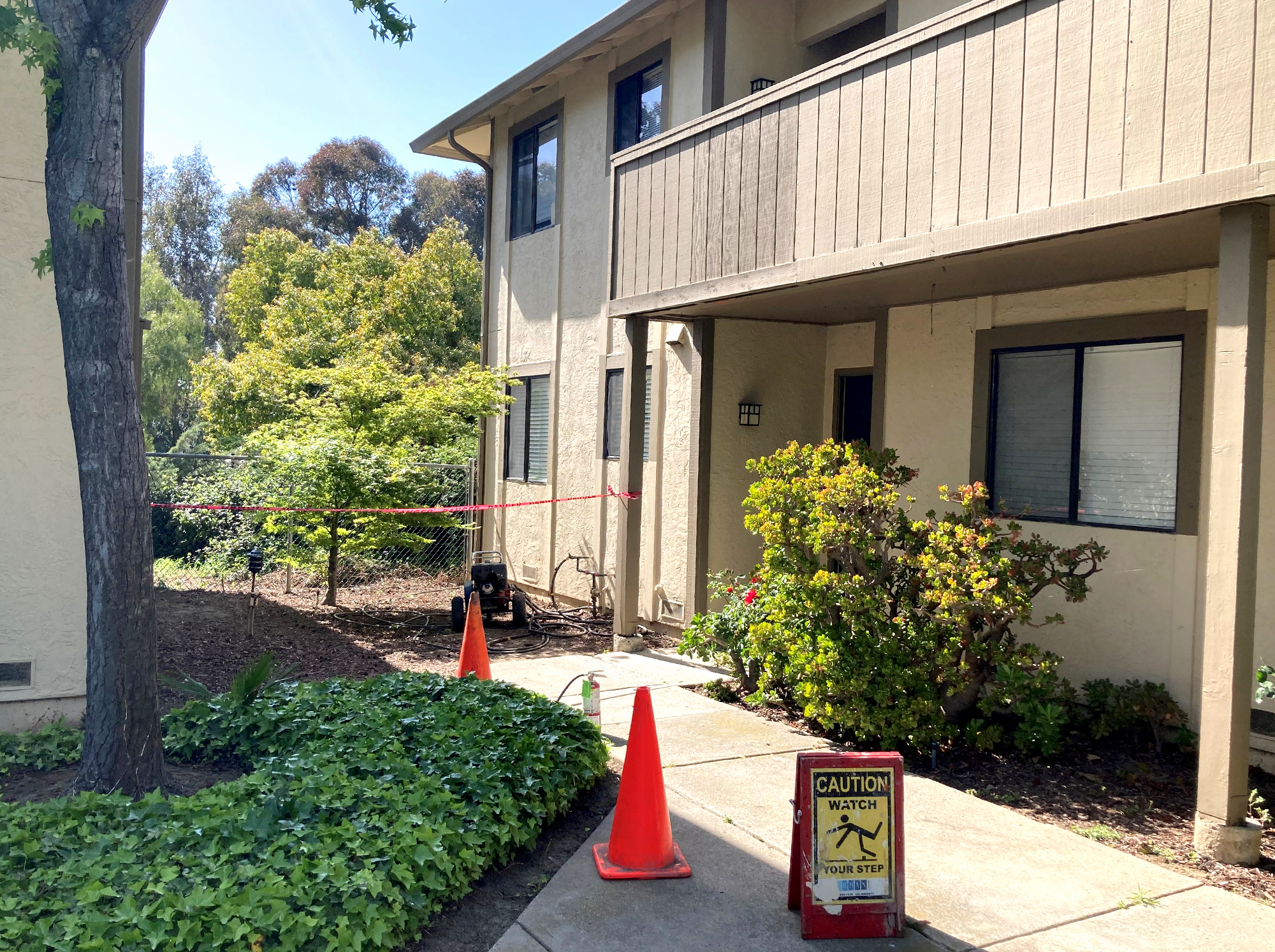
What We Did
Coated 200 units in 29 buildings, plus a pool house
Prepared and coated 29 carports, including trash enclosures
Coated over 100 balcony decks
Project Details
The scope of work here was to re-coat the building exterior, including a caulking tuneup at all locations where the caulking was failing. In addition, balcony decks were scheduled for the installation of a new acrylic maintenance coat.
This type of large-scale painting project is a specialty for a number of our crews and foremen. We begin with a careful safety map-out and handoff from the estimator to the production team and foreman. This way, any specific details about the project are communicated, and a solid safety plan to protect crew, residents, and property is developed and agreed upon.
After the map-out and safety gameplan, a schedule is sent to the HOA and construction manager so notices can be sent to residents so they know to close and secure windows when we are pressure washing their building and they can move items from their balcony decks.
Making sure decks and walls are well protected is important in any type of structure—maybe more so with wood substrates, where water bypassing the finishes can contact the wood, over time causing dry rot and structural issues for balcony decks. Unfortunately, we’ve seen many times where a relatively simple deck coating, one prep gets under way, and dry rot is located under the coating, turning into a large-scale support beam replacement project and blowing up the budget.
We have specialized crews that handle each step of the process, so fortunately we aren’t impacting one area for too long. Once we start, we work continuously on a building, utilizing these specialized crews in sequential order. The spray guy doesn’t mask, and the masker doesn’t spray, and whenever we spray, we always backroll.
This is a crucial extra step that not all contractors perform; it does add labor, but it ensures that all of the paint gets forced into the peaks and valleys of the substrates, ensuring a good bond to the substrate below. After the body coat is sprayed, the trimmers follow to paint the trim fascia and other trim elements.
In this case, the deck coating team follows the paint team. As a maintenance coat, the Westcoat MACcoat system is an outstanding acrylic option and offers the needed durability and resistance to foot traffic, outdoor furniture impact, and harsh UV rays. The decks are first thoroughly washed, and then any patching of loose coating is performed. With a sound substrate, the epoxy interlaminate primer is applied, then a topcoat with sand broadcast for non-slip is installed, and finally a finish coat of Westcoat SC10 is applied.
By the time we leave a building, it is complete and once again protected from the elements.
Want to know how we can help with your next project?