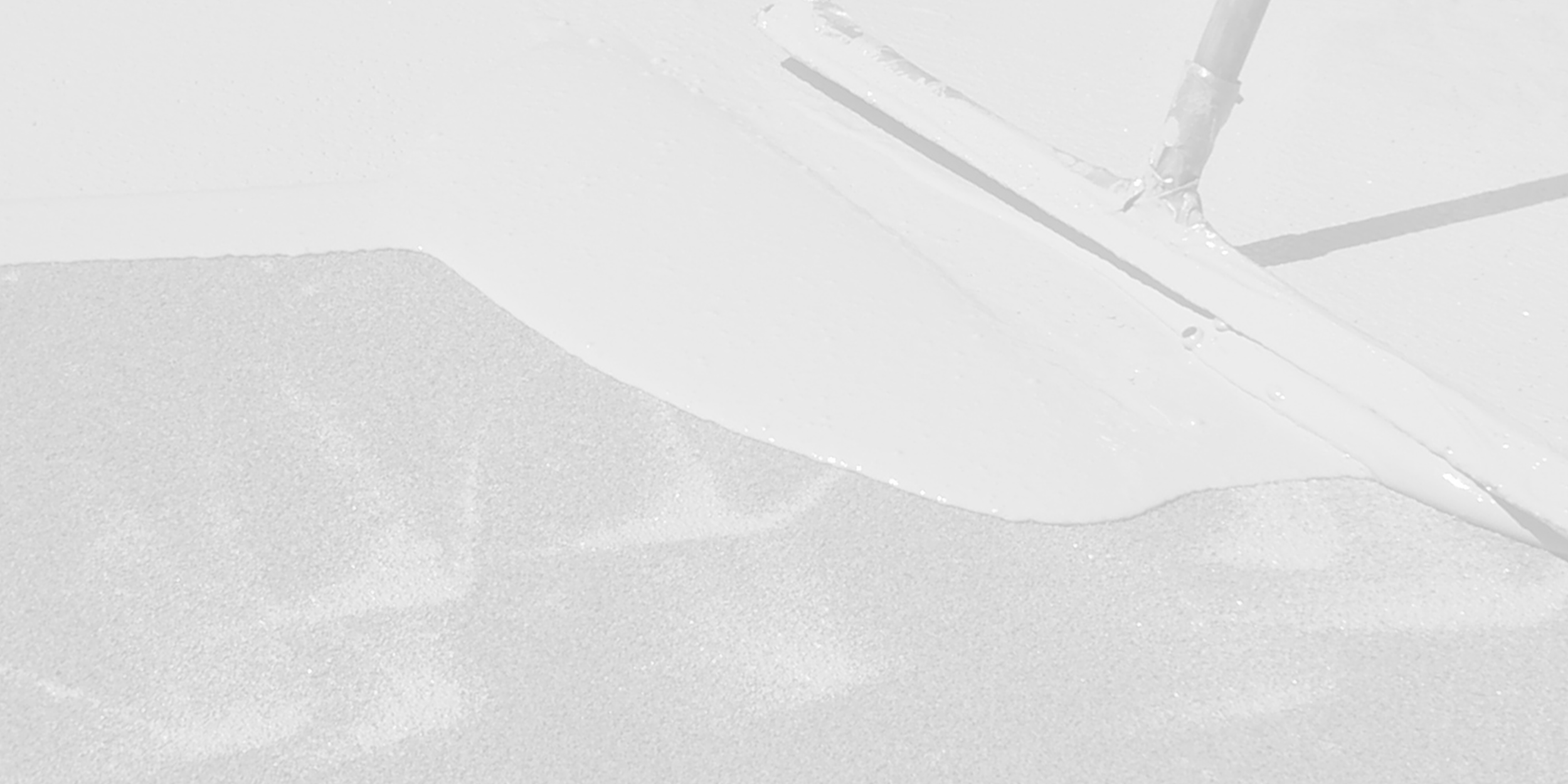
Traffic Coatings
Traffic coatings protect the substrates underneath as well as ensure the safety of pedestrians and cars alike. Over time, concrete surfaces can crack allowing water to work its way through the concrete causing structural integrity issues and allowing chloride-laden water to drip onto cars below.
Traffic coating should be inspected every 5 years. Depending on environmental conditions such as weather and traffic, they may need to be replaced every 10-15 years.
Why Invest In Traffic Coatings
Horizontal surfaces are more prone to collecting water than vertical surfaces
& need specialty coatings designed for longer term exposure to water.
Traffic coatings are applied to both walking and driving surfaces to protect the underlying concrete or wood substrate. Over time, concrete on the surface can crack, allowing water to contact the steel reinforcing - this can cause the crack to grow and the concrete to spall, resulting in structural integrity issues for the building. Water can also work its way through the concrete, and on a parking deck, dripping chloride-laden water onto cars below.
Wood substrates can get dry rot over time, weakening structural beams and decking, posing a safety hazard for pedestrians. For both applications, the system must include a wear coat with embedded aggregate to provide a safe, non-skid surface.
Surface preparation is a critical step. Concrete substrates need to have an adequate profile for the new coating to adhere properly, especially with vehicular traffic. A shortcut here can mean that you will have to re-do the coating too soon, a costly and time consuming mistake if you don’t start with the right installation team.
If you see bubbles and tears in the coating, they should be repaired as soon as possible. Once water gets under the topcoat, it can cause damage to the underlying coats, triggering a much more expensive and involved repair.
For large parking structures, we recommend a phased installation to minimize downtime. You’ll need to factor in time for the finished coat to dry because if you resume usual traffic too soon it will put stress on your coating, ultimately weakening its longevity sooner than needed.
Another option to maintain the longevity of your traffic coatings is to apply a maintenance coat. That means instead of taking off the coating down to the bare substrate, you can apply a maintenance coating as long as the original coating was well installed over a properly prepared substrate. Hence the importance of choosing a trusted and experienced installation partner from the start.

Types of Buildings We Work On
SUCCESS STORIES
We don’t work without our amazing clients!
Services
-
These are parking structures or parking decks. Product selection is important here, as these coatings are under pressure from wheels turning on them. Additional coats are often applied in drive lanes. These projects almost always involve traffic striping when finished.
-
These are usually concrete or wood and require a lighter-duty need than vehicular coatings. Detailing is key here, especially on wood decks where plywood seams flex and metal edge flashing are applied at the deck edge, all of which require extra reinforcement.
-
These decks typically need a faster turnaround so special fast cure traffic coating options are used most of the time.
-
The industry standard for vehicular decks, these are typically two-part products - though there are 1 part varieties. Usually available in only a few standard colors, the topcoat of these systems is hard and UV resistant.
-
Epoxy coatings are often used in mechanical rooms, kitchens, and labs. Mostly used in interior applications, these are very hard coatings where not a lot of movement is anticipated.
-
These coatings are a great option for pedestrian and balcony decks. Not only are there typically more color options, but it is also generally an easier and faster application.
-
These are used most often on slabs in contact with the ground to block water vapor from evaporating up from the soil through the slab where it can cause floor covering to delaminate.
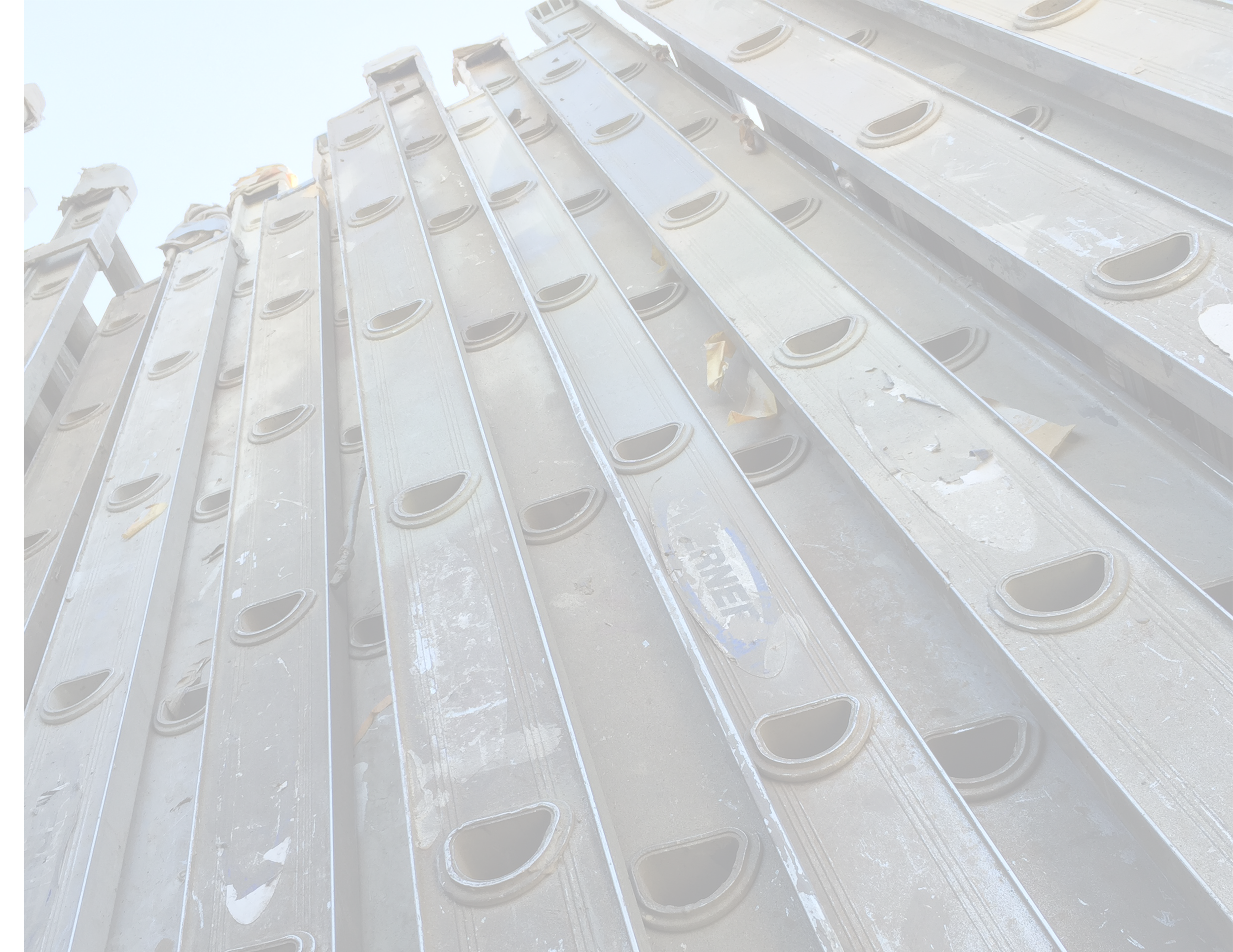