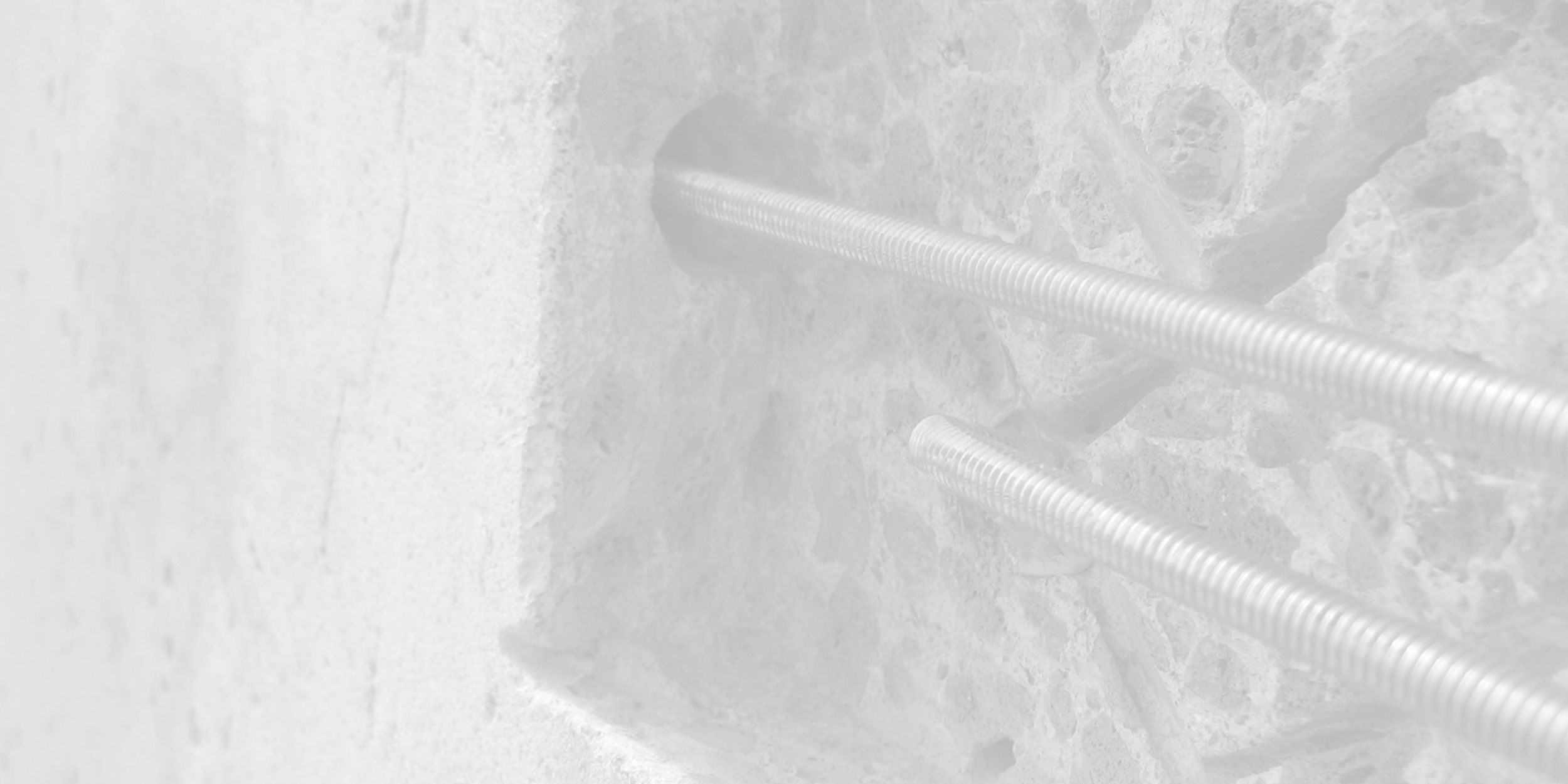
Substrate Repairs
Keeping the structural integrity of your building intact is key to ensuring it retains long term value as well as protecting public safety. If the building is compromised structurally it will be weak and real damage can be done.
Wood, concrete, stucco, EIFS, precast panels, and other substrates need to be maintained, and repaired when damaged and all building substrates and the coatings that cover them should be inspected annually for weak points, breaches, or gaps.
Why Invest In Substrate Repair?
Compromised building substrates can pose structural risks and safety issues. Loose, detached building elements are in danger of detaching from the building, falling onto pedestrians below, or damaging other property.
Voids, gaps, or breaches in a building substrate can allow moisture to bypass the envelope, damaging structural elements and damaging interior finishes. New coatings and other repairs won’t reliably stick to a damaged substrate, so not only do they pose a safety risk but you will have to pay for repairs twice.
Concrete substrates can crack, or spall, if water is allowed to enter through cracks and contact the steel reinforcing. The steel expands, cracking the layer of concrete above to become loose and eventually detach from the building.
Wood substrates suffer from dry rot if exposed to moisture for a long period of time. While unsightly at building trim elements, dry rotted deck support members pose a serious safety threat if the deck becomes so weak it collapses.
EIFS substrates are comprised of foam, a then layer of cementitious base coat, reinforcing mech, more basecoat, then a topcoat. In profile - maybe a ¼ inch thick. While attractive and lightweight, this is a system vulnerable to dents and punctures. Once punctured, and water is allowed behind, further damage can be caused, causing more delamination and damage to interior surfaces.
Stucco substrates need to be kept intact to avoid excessive moisture contacting the building paper used as a waterproofing layer. In a traditional stucco installation, the paper is attached to cladding with staples, and the metal lathe is also attached (over the paper) using fasteners. All of these small attachment points are potential pathways for water to contact and weaken the cladding behind.
What to look for when it comes to substrate repairs:
Locating Spalls
Locating spalls in concrete takes an expert eye – and ear. We often use the hammer-tap “sounding” technique to listen for hollow spots or voids in the concrete. This provides information on the approximate dimensions of the spall, and where to begin removing disbonded concrete.
Treatment of Steel Reinforcing
As almost all spalls are caused by corroded steel reinforcing (rebars), its treatment and protection is paramount. Treatment of steel reinforcing includes 1) removing existing corrosion or replacing the reinforcement if necessary, 2) application of corrosion inhibitor on the steel reinforcement, and 3) providing adequate concrete cover to provide adequate protection from the elements.
Texture / Color Matching
In instances where repair patches will not be coated after the repair is complete, it is important that the texture and color are matched to the surrounding area as much as possible. Different floats and trowels, in the hands of an expert, are used to achieve a wide range of stucco, EIFS, or concrete finishes. Mockups are important for the project team to make sure the desired results are acceptable and achievable.
Mockup / Testing of Repairs
Before a final repair protocol is defined, sometimes a test repair is required. In addition to covering all steps of demolition, preparation, and installation, it offers a chance to verify the strength of the final repair. This also helps set expectations for occupants who are impacted by the repair, and contingency plans can be developed where necessary.
Protecting Adjacent Surfaces
Protection of adjacent surfaces is especially important during the demolition phase. Oftentimes, glass and aluminum are adjacent to the repair, requiring special attention for protection. In addition, demolition on vertical surfaces, especially on high-rises, requires protective netting under the spall and an extra pair of hands to catch large pieces of concrete that are dislodged during demolition.
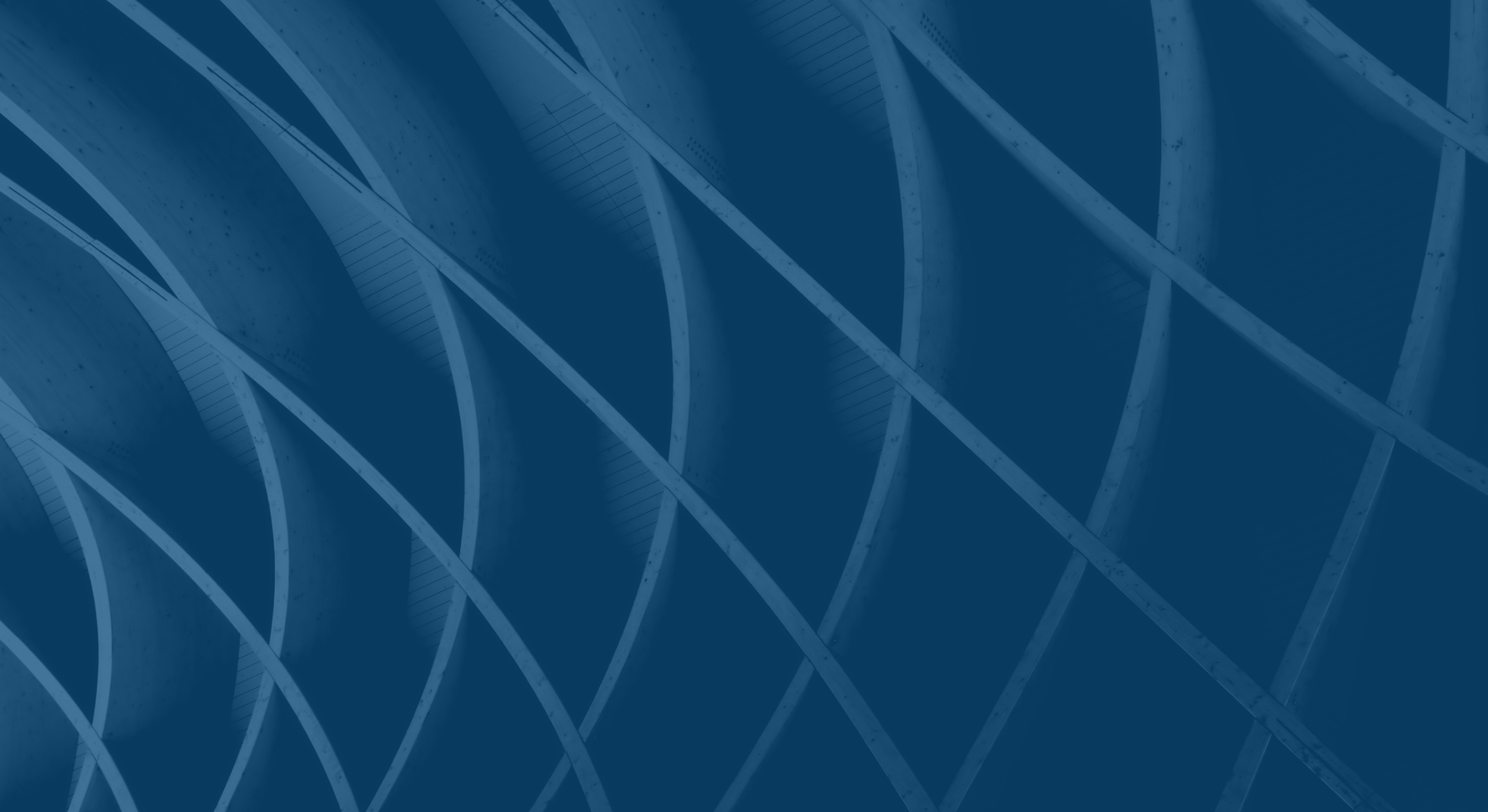
Types of Buildings We Work On
SUCCESS STORIES
We don’t work without our amazing clients!
Services
-
This is the location and repair of loose / delaminated concrete elements on a concrete facade.
-
Repair of punctures, cracks, and lamina damage to the EIFS substrate. Typically, this includes the installation of new foam, reinforcing mesh, basecoat, and topcoat.
-
Spalls and cracks in stucco need to be repaired to prevent the waterproofing layer beneath from being overwhelmed. Includes the integration of new building paper, a metal lathe, and stucco patches.
-
Includes the replacement of dry-rotted trim, fascia boards, and siding. More involved repairs include replacement of deck structural members and installation of new decking and flashing.
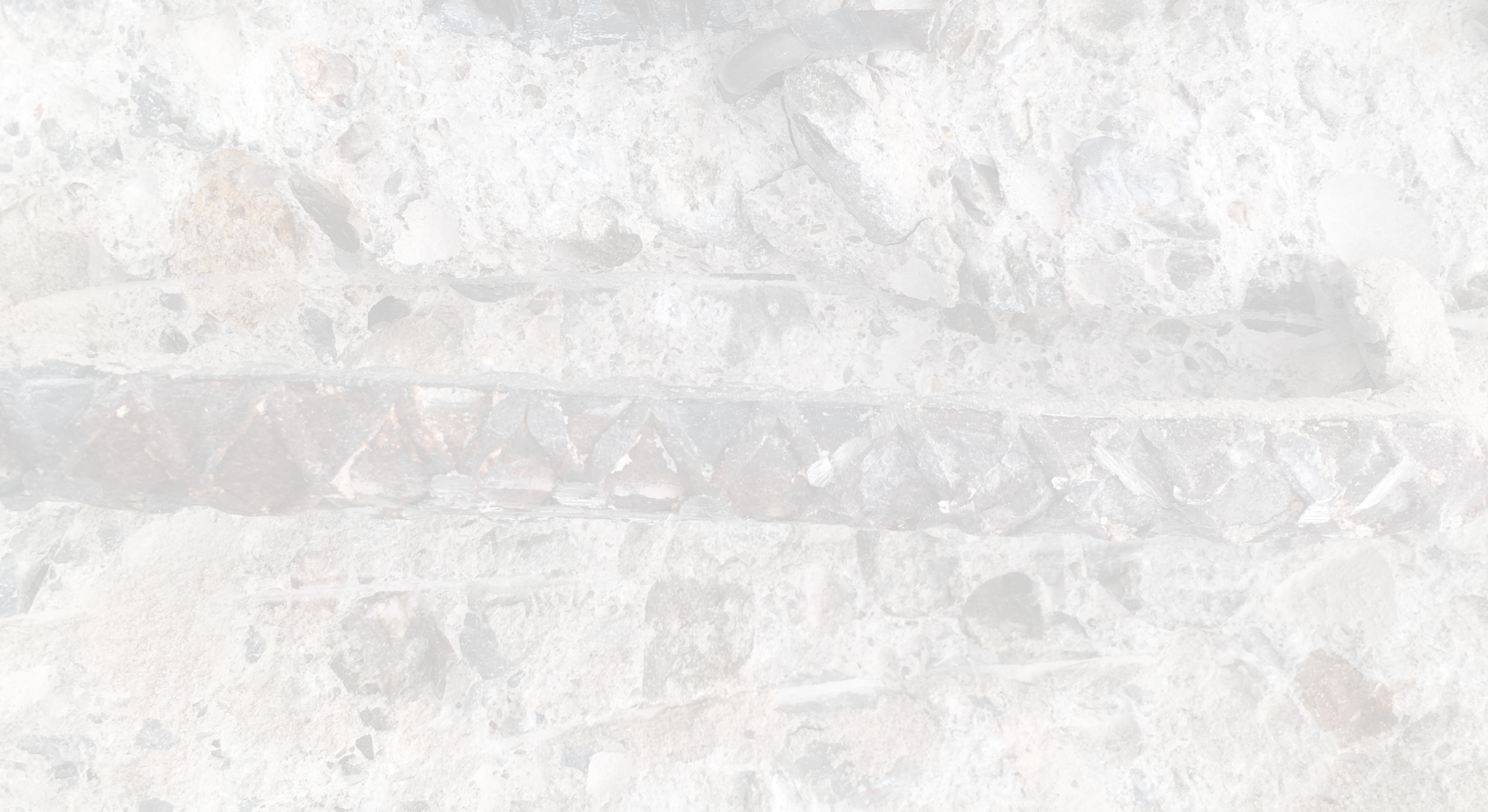