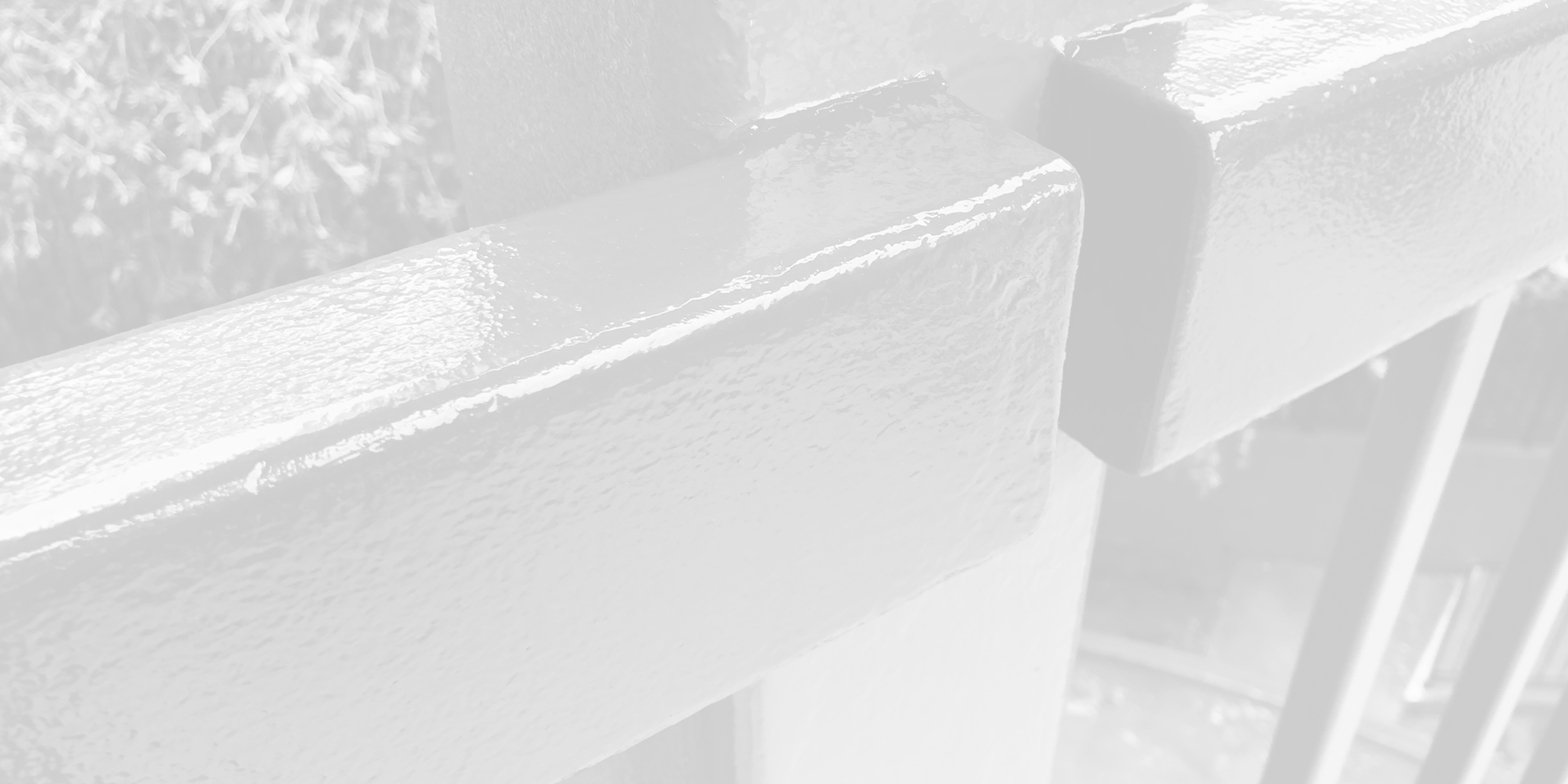
Metal Coatings
Metal surfaces require special detailing and materials - different than wood or masonry. In most cases, metal can experience much larger temperature fluctuations, and needs high performance coatings to accommodate.
Metal coatings should be inspected every five years or so for areas of rust or failure.
Why Invest In Metal Coatings?
While some metal panels are decorative, and damage is more of an aesthetic issue, deteriorated handrails or metal supports pose safety risks.
Maintaining a sound coating on metal surfaces helps prevent rust and oxidization, or other deterioration of the metal substrate. Uncoated metal, over time and through exposure to moisture and UV rays, can rust, corrode, or experience pitting.
Once rust begins, it’s almost impossible to remove it completely. Besides being unsightly, rust can eventually corrode metal elements, such as handrails, all the way to complete failure, causing a safety hazard.
Most metal coatings are applied thinner than their masonry or wood counterparts. Careful detailing and prep of metal is key since the coatings don’t soak into the substrate to create a bond - they rely on a mechanical bond achieved through surface profiling.
Some things to consider to set your project up for success:
Oftentimes, the budget doesn't allow the complete removal of the existing metal coating before applying a new one. Removing loose existing coating, spot priming, and top coating with new is an option often selected by HOAs, but the new coating is only as good as what it’s sticking to.
Metal must be coated in the right conditions - coating metal in the wintertime, when temperatures can hover or get below 40 degrees is not advised, since the new coating can’t fully cure.
There are viable rust inhibitive primers for situations when not all rust can be removed. It is worth it to invest in the best quality primer, installed by experienced professionals, to minimize future maintenance issues.
Some high performance coatings need extensive prep, such as sandblasting in order to perform correctly and qualify for manufacturer’s warranties. Consider how much performance your coating needs.
Two-part urethane metal coating is a top-of-the-line metal topcoat, but in most cases, since it is a two part, catalyzed material, challenging for in house staff to touch up. Consider the maintenance program when selecting a metal substrate top-coat.
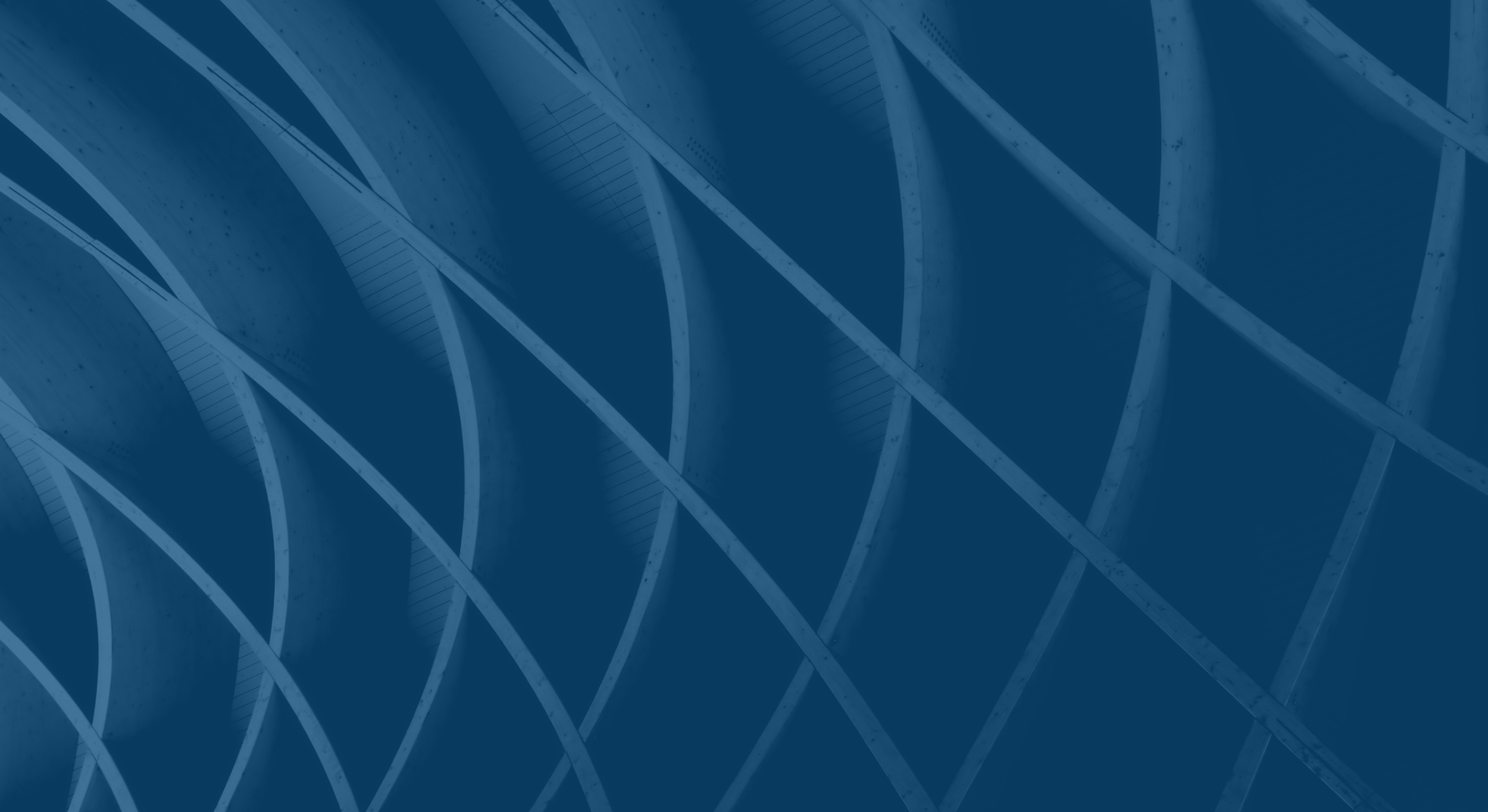
Types of Buildings We Work On
SUCCESS STORIES
We don’t work without our amazing clients!
Services
-
These are typically single-part coatings, specially designed to be applied to metal surfaces without a primer. DTM coatings provide a durable finish on metal surfaces and are great options when two-part coatings are not required. DTM coatings are also much easier to maintain since no special mixing is required.
-
Epoxy undercoat with urethane finishes are top of the line systems for metal surfaces. Preparation and materials costs for these systems can be expensive but are worth the investment for their long term performance. These systems can be more expensive to maintain and are generally not recommended in situations where in-house staff will need to do regular touchups.
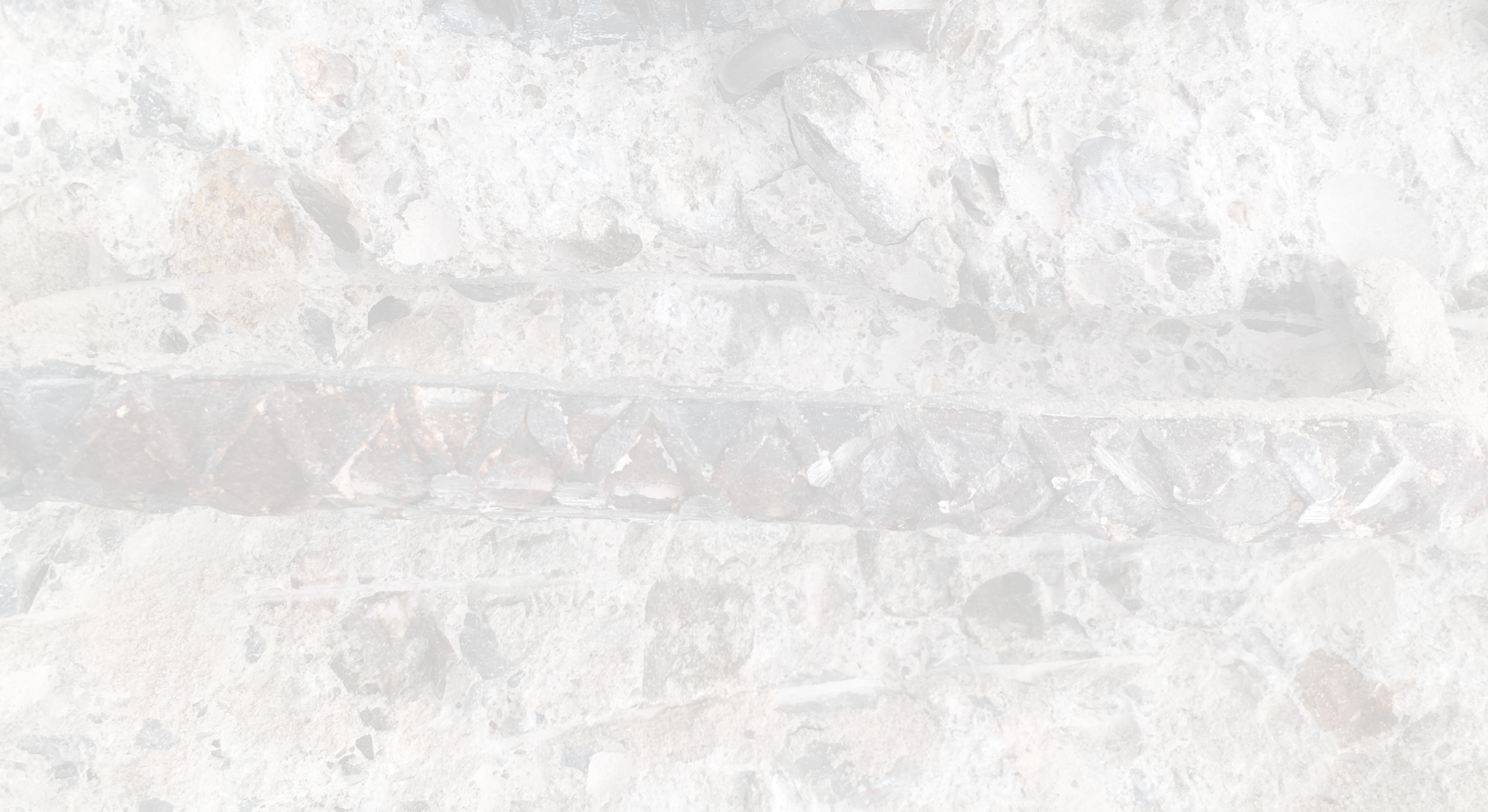